Precision Levelers for Flame Cut Parts (Plasma and Oxyfuel Cut Parts) and Heavy Plates
In the metalworking and manufacturing industries, ensuring the flatness and precision of cut parts is essential to maintain the integrity and performance of the final product. When dealing with flame cut parts, including plasma-cut and oxyfuel-cut parts, as well as heavy plates, achieving the desired level of flatness and stress relief is a critical challenge. Precision levelers are designed to tackle this problem effectively by flattening and stress-relieving these materials in a quick and efficient manner.
These precision levelers can process parts and plates with thicknesses ranging from 4 mm to 16 mm, making them an ideal solution for both thick plates and rough, rusted parts. By utilizing a series of alternating bends, the machine not only flattens the parts but also helps relieve residual stresses caused by the cutting process.
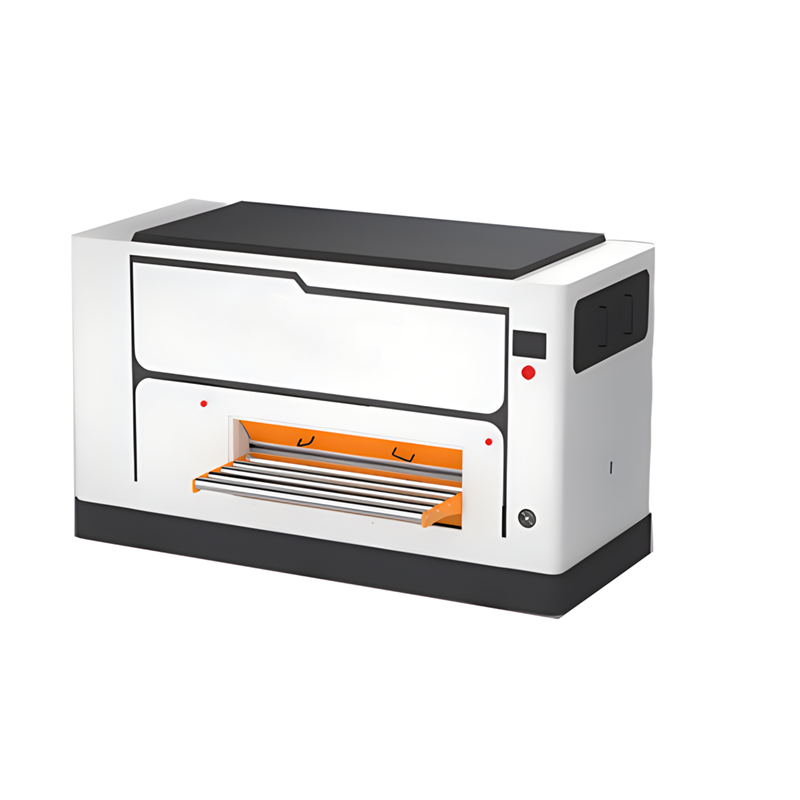
Key Features and Advantages
1. Material Thickness Range: 4 mm to 16 mm
The precision leveler is specifically designed for processing flame cut, plasma cut, and oxyfuel cut parts that range in thickness from 4 mm to 16 mm. This makes the machine ideal for handling both medium and heavy-duty materials commonly used in various industrial applications, such as the automotive, construction, and metal fabrication industries.
For thinner plates (4 mm to 6 mm), the machine uses moderate pressure to remove warping and ensure flatness.
For thicker plates (6 mm to 16 mm), more pressure is applied to effectively level heavy plates without damaging or over-straightening them.
2. Passage Widths Available: 400 mm to 3800 mm
The precision leveler offers a wide range of passage widths, from 400 mm to 3800 mm, allowing it to process a variety of sheet sizes and large plates. The machine can handle both small and large parts, ensuring versatility in production lines that deal with different material sizes. This flexibility makes it suitable for batch processing of parts in varying dimensions or high-volume operations.
Smaller widths (400 mm to 1000 mm) are perfect for smaller parts or precise leveling in narrow sheet metal applications.
Larger widths (1200 mm to 3800 mm) are capable of handling larger and heavier plates, ensuring that even large structural plates and panels can be leveled efficiently.
3. Efficient Leveling of Flame Cut Parts
Plasma cutting and oxyfuel cutting processes are often associated with significant heat-affected zones (HAZ), which can lead to material distortions and residual stresses in the cut parts. Precision levelers are designed to quickly remove these distortions by applying a series of alternating bends to the material. This technique allows flame cut parts to be leveled in a matter of seconds, unlike traditional manual flattening, which can take from several minutes to hours.
The alternating bending process ensures that each part is subjected to controlled deformation, which straightens out the internal stresses and flattens the material with minimal risk of damage.
This high-speed process results in a significant reduction in production time, making it ideal for high-throughput manufacturing environments.
4. Rough Plates with Rust and Dirt
The precision leveler can also handle rough, rusted, or dirty plates. Parts that have been exposed to environmental factors or heavy usage may accumulate rust, dirt, or scale on their surfaces, which can interfere with downstream processes. The leveler effectively handles these materials by applying sufficient force to straighten them, even if they are contaminated with rust or other debris. This feature reduces the need for additional surface preparation before processing.
The machine is equipped with heavy-duty rollers and adjustable pressure settings, making it capable of processing materials that are not in pristine condition without damaging them.
This capability is especially useful in industries dealing with scrap metal, recycled steel, or parts that have been stored outdoors.
5. Low-Stress and High-Flatness Results
The leveling machine is designed to provide low-stress and high-precision results, which are critical for ensuring that parts meet the exact flatness requirements for further processing. After leveling, parts are stress-relieved, making them less prone to warping during welding, painting, or other post-leveling processes.
The low-stress leveling ensures that the material retains its structural integrity, preventing it from becoming overly deformed or weakened.
The high flatness achieved by the machine allows parts to fit together seamlessly in subsequent manufacturing stages, whether in welding, assembly, or coating.
6. Automated Process
The precision leveler is equipped with automated control systems, which significantly reduce the need for manual intervention. With this automation, the machine can handle large volumes of parts and ensure consistent results, even in high-output environments. The machine can be programmed to adjust parameters such as pressure, speed, and roller gaps based on the material type and thickness.
The user-friendly interface allows operators to quickly set up and monitor the leveling process, improving efficiency and reducing the likelihood of human error.
Real-time adjustments to the process ensure that the machine can adapt to different materials and thicknesses, providing optimal performance across various production runs.
7. Applications
The precision leveler is widely used in industries where high-quality flat parts and plates are essential. Key applications include:
Metal Fabrication: For leveling parts that will be used in the production of machinery, structures, or other fabricated metal products.
Automotive Manufacturing: To ensure that car body panels, chassis, and structural components are flat and ready for assembly or welding.
Construction: For leveling heavy plates used in the construction of buildings, bridges, and industrial structures.
Shipbuilding: To flatten large steel plates used in the production of ships and other marine structures.
Aerospace: For processing metal parts that require high precision and minimal distortion to meet safety and performance standards.
Heavy Equipment Manufacturing: For leveling thick plates used in the production of industrial equipment, machinery, and other heavy-duty components.
8. Time Efficiency
One of the primary advantages of precision levelers is their speed. While manual flattening can take anywhere from several minutes to several hours, the automatic leveling process can level flame cut and heavy plates in a matter of seconds. This drastic reduction in processing time allows manufacturers to increase throughput and improve productivity.
Increased throughput translates to faster production cycles and improved efficiency in high-volume manufacturing settings.
Reduced labor costs are a result of the automated process, reducing the need for manual handling and supervision.
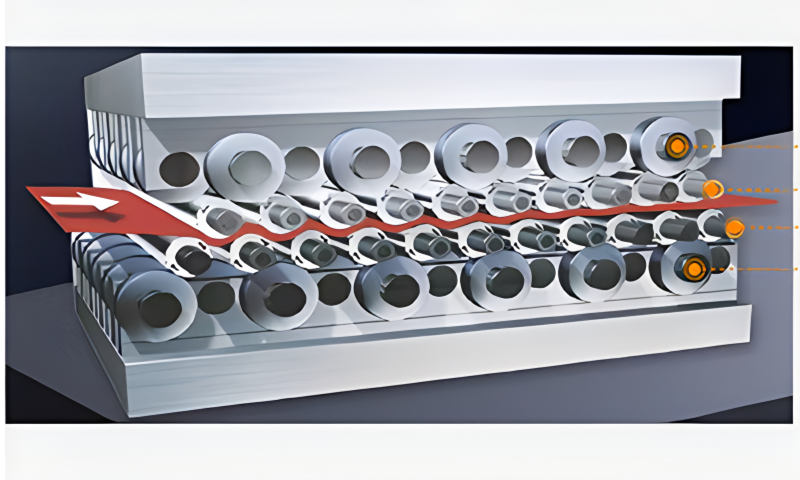
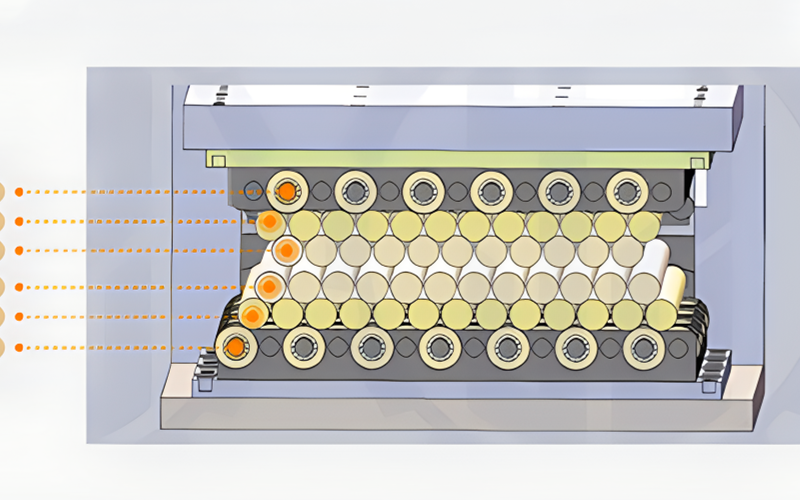
The precision leveler for flame cut parts, including plasma-cut and oxyfuel-cut parts, is an essential tool for industries that require flat, stress-relieved, and high-precision materials. With the ability to process materials ranging from 4 mm to 16 mm in thickness and passage widths from 400 mm to 3800 mm, these machines are highly versatile and can handle both small and large parts efficiently. The alternating bend process applied in the leveling machine ensures fast, low-stress results, even for rough, rusted, or dirty plates. With automation, high flatness, and stress-relief, the machine is perfect for industries such as automotive, construction, metal fabrication, and heavy equipment manufacturing. By improving flatness, reducing production time, and minimizing manual labor, these machines provide manufacturers with a powerful solution for leveling laser cut, plasma cut, and punched parts.
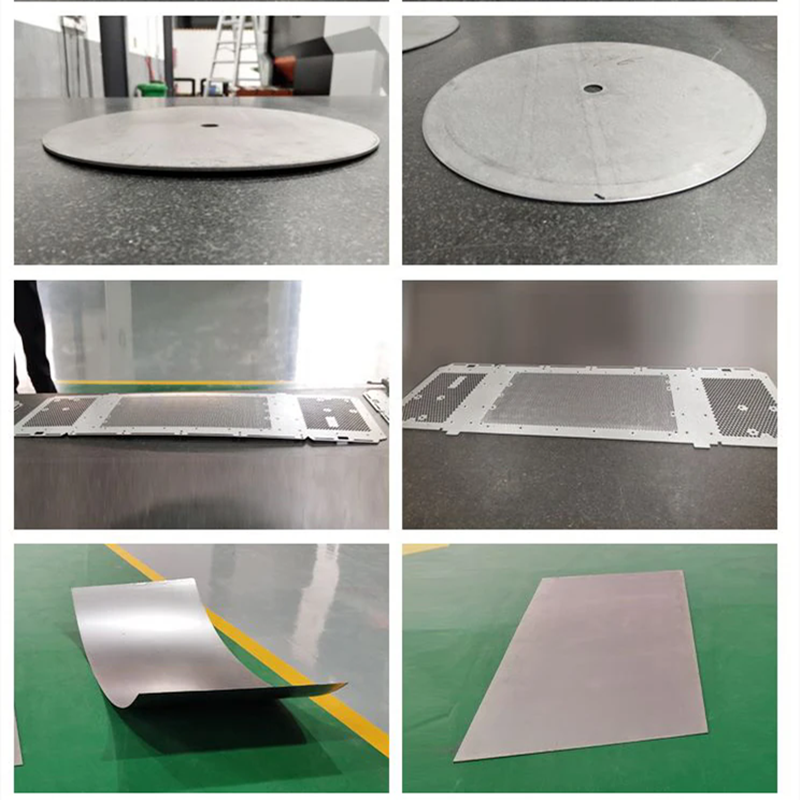
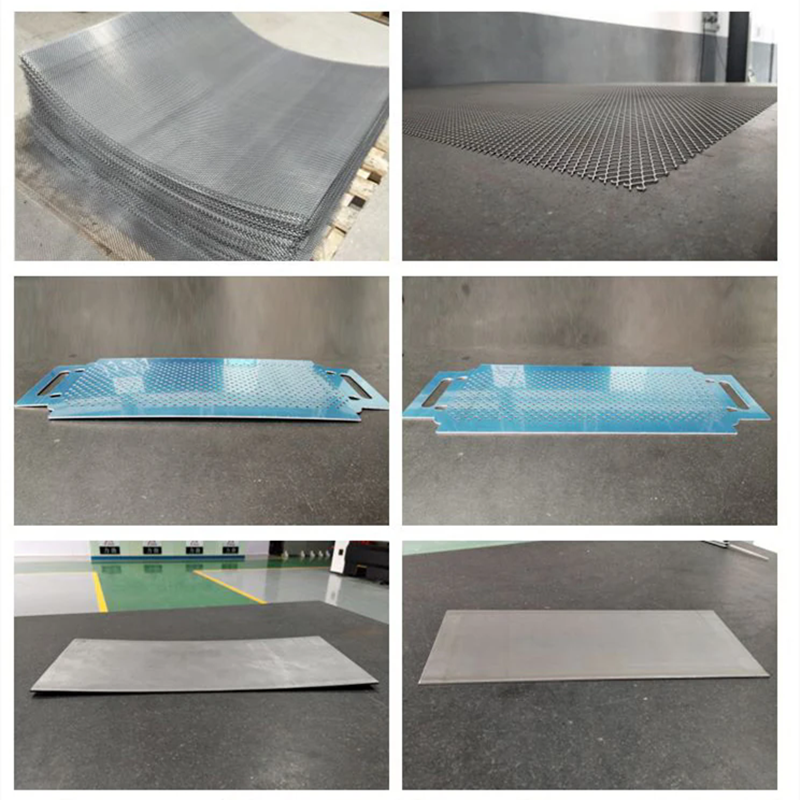